Good to know
Selecting the right tape for your needs
Many different factors play an important role in finding the right material. Specific characteristics of the materials, environmental factors, application/installation conditions, cost and performance requirements must be considered.
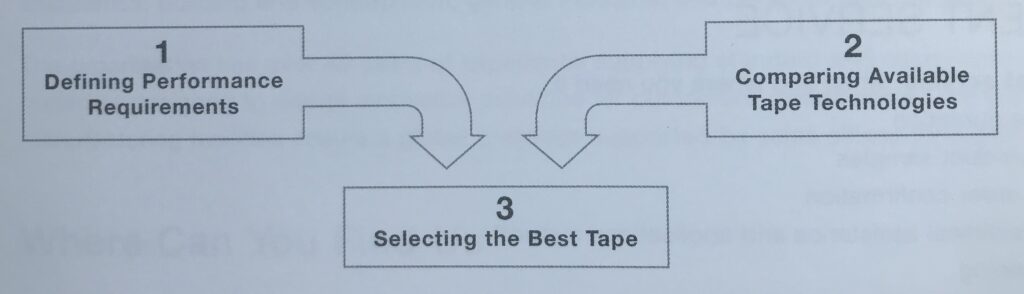
The first steps are to define:
Type of substrate
The surface energy of the material affects the ability of the adhesive to spread over the substrate. Materials with low surface energy make it difficult to get a good bond, while those with high energy provide the best adhesion.
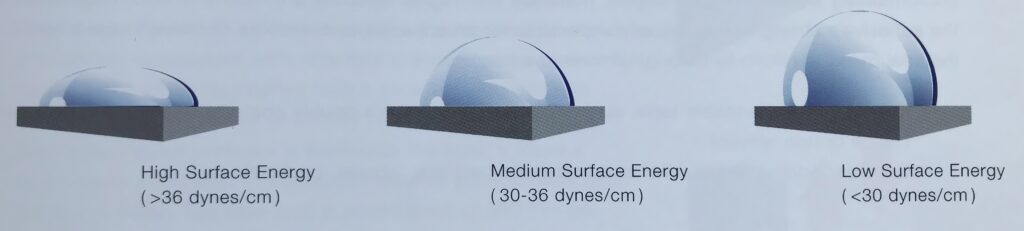
The surface texture can affect the bond strength of the adhesive; materials with high roughness do not allow full adhesion of the adhesive to the substrate (poor contact + small surface area = low bond strength).
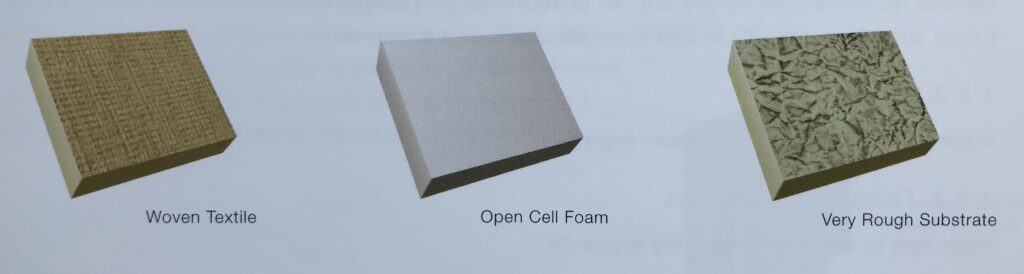
In the case of materials with a large grain size, an improvement in the adhesive strength can be achieved with the appropriate selection of products:
– heavier adhesive mass allows for more flow into material,
– softer adhesives have better flow properties,
– a more aggressive adhesives maximizes bond strength at contact areas,
– a more flexible tape conforms to textured materials.
Surface contamination prevents effective bonding. There are many types of surface contamination – some are not visible to the eye, but can be identified analytically. Simply cleaning the surface (washing or flame treating) will ensure an effective bond.
The contour of the substrate will influence both the adhesive selection and the product selection. For conformability around irregular angles, materials with higher flexibility are recommended.
Environmental conditions
The temperature of the substrate and adhesive during application or lamination is an important factor affecting the quality of the bond. A minimum is generally recommended 10oC.
The temperature to which the finished product will be subjected during operation must also be taken into account. General recommended ranges are: -40 to 180oC for (UV) acrylic based adhesives, -25 do 110oC for rubber based adhesives and -80 do 250oC for silicone based adhesives.
Another important factor is humidity (duration and intensity of moisture exposure), outdoor conditions (from indoor to extreme weathering exposure), exposure to chemicals (including solvents, cleaning agents and fuels) and UV exposure (direct or indirect).
Required bond strength
Adhesives have many performance characteristics, which are specified and measured depending on the end application. Three commons performance characteristics:
– adhesion – the molecular force of attraction or bond between the adhesive and the surface it is in contact with. It is determined by the material’s surface energy and chemical make-up of the adhesive.
A pressure-sensitive adhesive’s measure of performance is expressed in N/25 mm, as the tape is pulled at a 180o, 300 mm per minute. Usually off a polished stainless steel panel. A 90o version of this test is used when testing foam carrier tape adhesion.
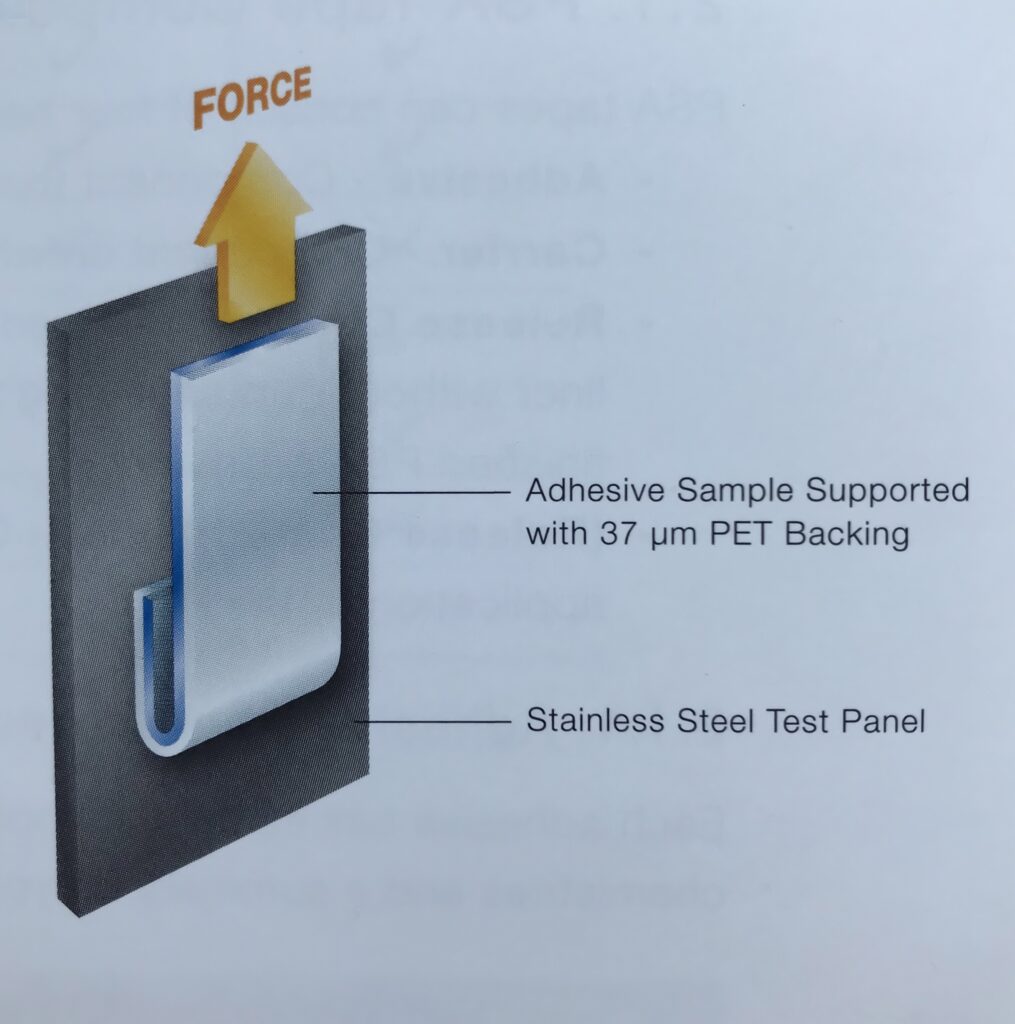
– tack – the property of a pressure-sensitive adhesive thet allows it to adhere to a surface with very light pressure and a minimum contact time (often referred to as “quick tack). During testing, no pressure is applied to the tape.
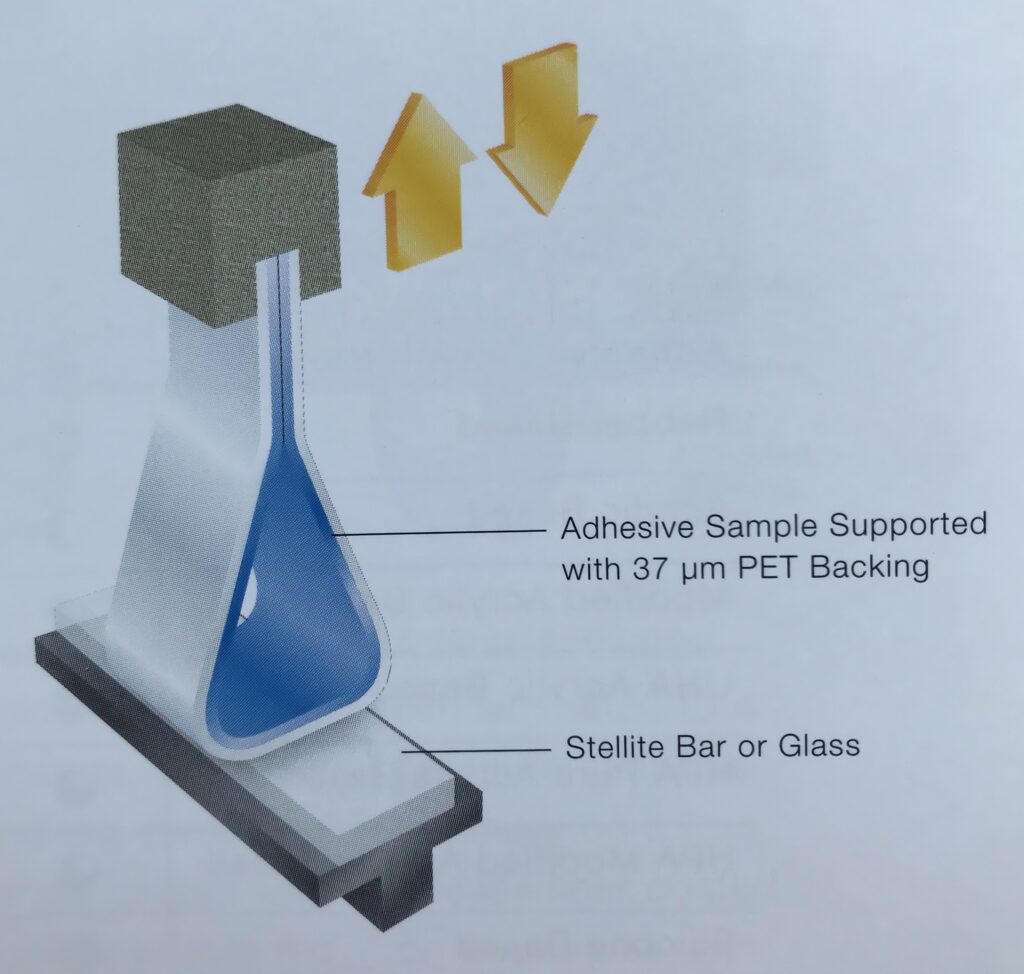
Instead a loop of tape is lowered to a stainless steel or glass surface until contact is made. The tape loop is pulled back at 300 mm per minute.
– cohesion – refers to the internal strength of an adhesive and its ability to resist splitting or slippage caused by external shear forces. Cohesion is measured by its resistance to forces parallel to the surface.
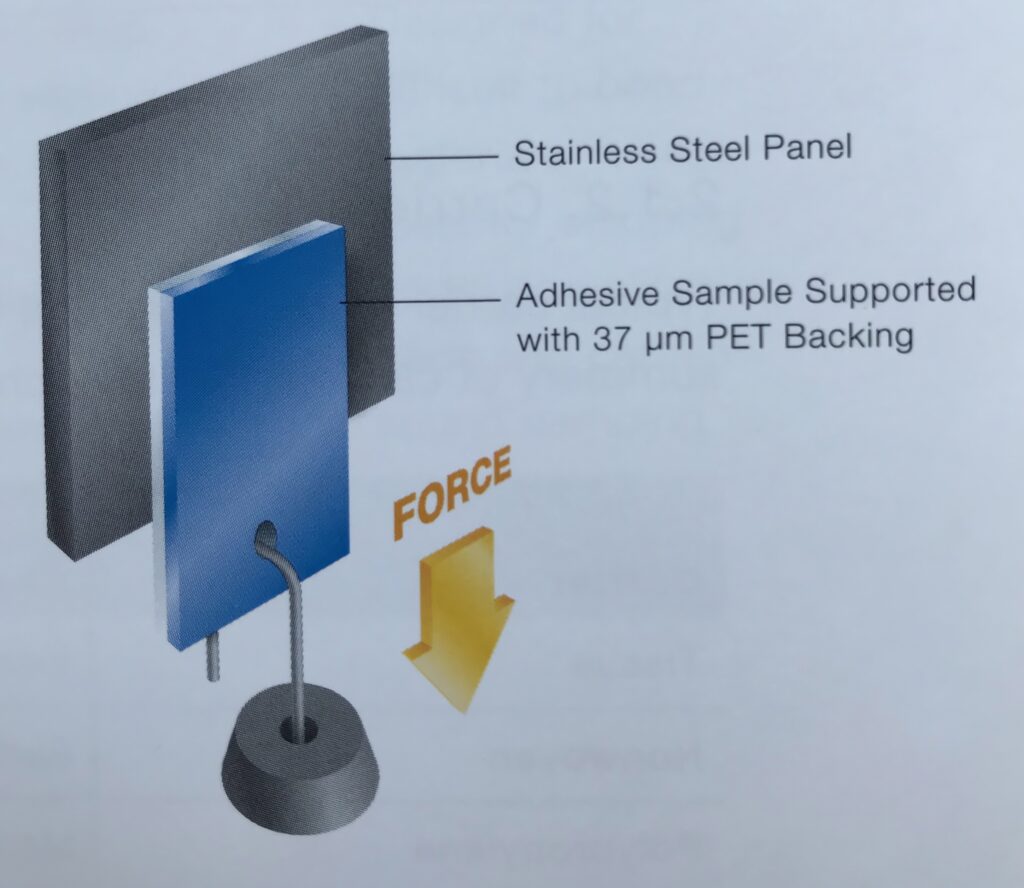
Measurement is given in minutes until failure and/or distance slipped. Shear can also be measured in a Dynamic Shear test (clamp moving 2 mm/min).
PSA constructions
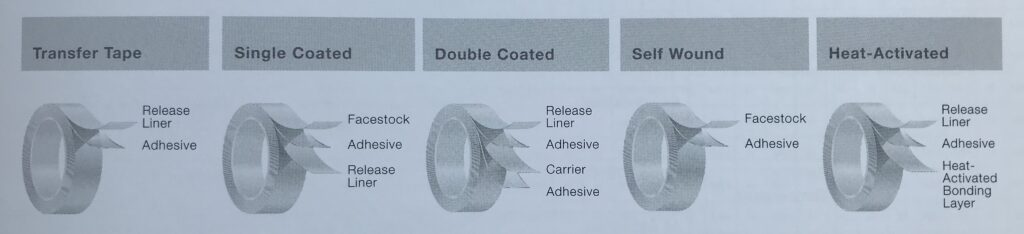
Transfer tape
A film of unsupported adhesive is coated directly onto a siliconized realise liner. The liner is coated with silicone on both sides to ensure that the tape unwinds easily and can be laminated to various substrates.
– offers superior conformability,
– great for laminating materials,
– ideal for nameplate mounting and foam bonding.
Single coated
The adhesive is coated on one side of a carrier. A release liner coated on one side with silicone protects the adhesive.
– potential label stock,
– foil insulation tapes.
Double coated
The adhesive is coated on both sides of a carrier material. The construction is provided on a liner coated on both sides with silicone.
– offers improved internal strength,
– greater dimensional stability,
– easier converting,
– easily slit into narrow rolls,
– adds support to otherwise stretchy materials.
Self wound
The adhesive is coated on one side of a carrier. The other side of the carrier is generally coated with silicone to enable the tape to unwind easily.
– provides wrap around sealing,
– acts as closure system,
– potential label stock,
– can provide moisture vapor barrier.
Heat-Activated
A heat-activated film laminated to a pressure-sensitive adhesive on a release liner coated on both sides with silicone.
– designed for difficult to bond materials,
– ideal for shipping pads, non-slip step pads certain sound damping materials.