The increase in the level of corrosion damage has opened up new horizons for the durability and stability of reinforced concrete structures, especially in highly aggressive areas.
Various phenomena contribute to the corrosion of the reinforcement in the concrete.
Due to its natural alkalinity, concrete creates a protective environment around steel, but this environment is not eternal. Research shows that corrosion damage occurs when critical amounts of aggressive agents penetrate the pores in the concrete, attack and destroy the passivation protection around the steel, and expose rebar to corrosion.
There are two main types of aggressive factors that can cause this phenomenon:
Carbonization: Carbon dioxide and moisture in the surrounding air penetrate the pores of the concrete and lower the pH level to near neutral values. Under such conditions, rebar can cause corrosion;
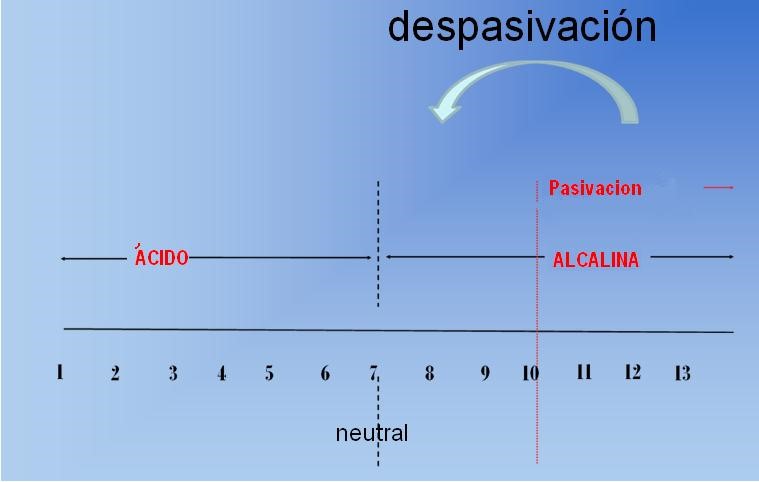
Chlorides: By penetrating into concrete, this type of aggressive agent can break the protection and cause local corrosion (pitting), even under alkaline conditions, which can even damage steel reinforcement.
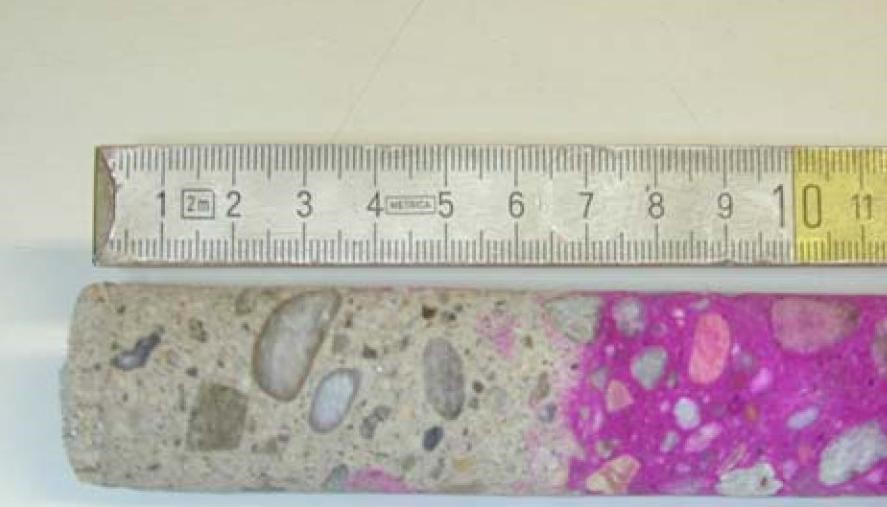
The rebar corrosion produced by these phenomena forms iron oxide (Fe2O3). Since iron oxide (rust) is much larger in volume than solid steel (5-6 times more), even a small loss of metal (e.g. ~ 0.1mm) from the surface of the reinforcing bars can cause enough corrosion products to generate internal stresses which will cause cracks and damage to the concrete.
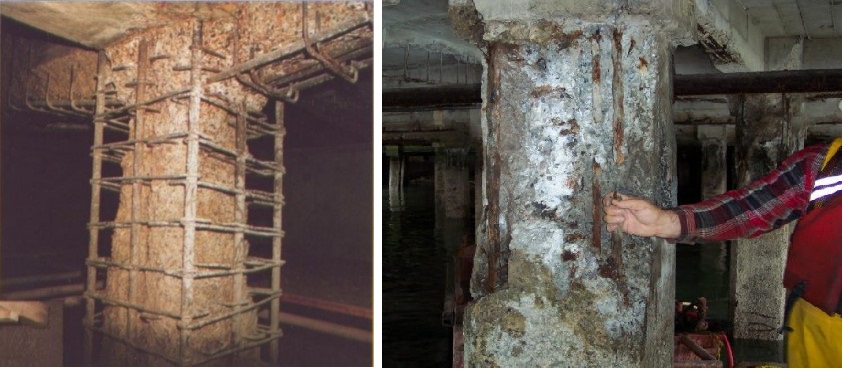
Chloride corrosion acts locally and is very destructive, it is undoubtedly the most aggressive and dangerous type of threat to the structural stability of a reinforced concrete element. Cathodic protection, both under the influence of current (ICCP systems) and the use of sacrificial anodes (GACP systems), helps to prevent the deterioration of reinforced concrete, and especially
in the latter case, allows us to reduce maintenance costs in the long term.
According to a 1981 report by the Federal Highways Administration – US Department of Transportation, cathodic protection (CP) is the only effective technique for repairing chloride-contaminated reinforced concrete structures and inhibiting corrosion, regardless of their level.
Thanks to the cathodic protection, the corrosion potential is transferred to the resistance zone and the corrosion process is completed. To apply cathodic protection, only the damaged concrete member needs to be removed and it is not always necessary to remove the solid, contaminated part.
SOLKAT company offers various types of zinc anodes, which perfectly protect both newly built and existing facilities. It is especially recommended for structures which are expected to have a long service life, especially in demanding conditions (such as bridges and viaducts, tanks, foundations, etc.).
Our solution does not require power supply from an external source (GACP system), which lowers the initial installation costs and also reduces the resources for long-term maintenance of related infrastructure. Available anodes and their dimensions in cm:
- SuperAnoda GSCslk 10/10 –> 10 x 5,5 x 1,2;
- SuperAnoda GSCslk 10/20 –> 10 x 5,5 x 1,5;
- SuperAnoda GSCslk 30/10 –> 30 x 5 x 1;
- SuperAnoda GSCslk 30/20 –> 30 x 5 x 1,2.
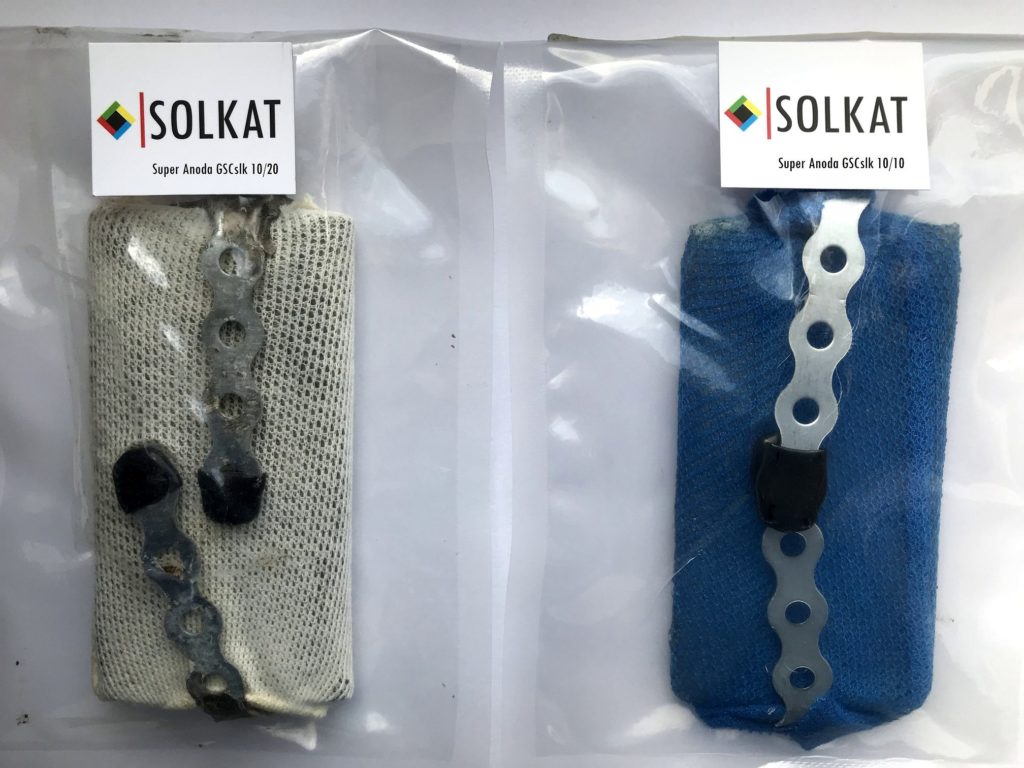
The size and arrangement of the anodes are fully dependent on local environmental factors, although all potential influences should be considered. The lifetime calculation is therefore only “best estimate”
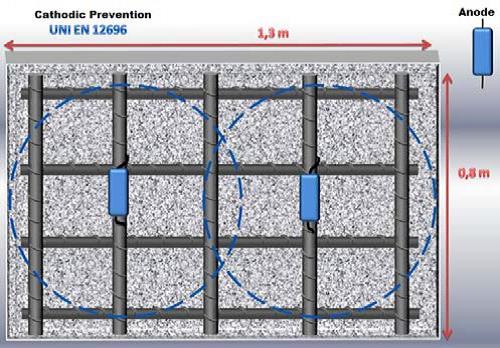
New structures
GSCslk 30/10 or 30/20: 1 pcs./m2 concrete;
GSCslk 10/10 or 10/20: 2 pcs./m2 concrete .
Old structures
GSCslk 30/10 or 30/20: 2 pcs./m2 concrete ;
GSCslk 10/10 or 10/20: 3 pcs./m2 concrete .
At your request, the anodes can be modified and designed to achieve a service life of up to 40 years .
More information on our partner’s website – Metalnastri S.r.l.: https://www.metalnastri.it/en/index.html